Critical Minerals Considerations For a Pacific Northwest Hydrogen Hub
Mitigating resource risk and accelerating Washington state’s energy transition
Produced by FP Analytics, with support from
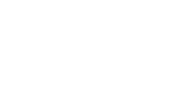
March 2023
After decades of development, hydrogen is finally poised for what market analysts have called “a breakneck growth pivot” due to a confluence of supportive policies, rising energy security concerns, and the growing urgency of addressing greenhouse emissions from “hard to abate” sectors like heavy duty transportation, shipping, and industry. In the U.S., the Bipartisan Infrastructure Law (BIL) will invest $7 billion in funding to develop up to ten regional hydrogen hubs that bring together hydrogen production and end users. For the next decade, the Inflation Reduction Act (IRA) offers tax credits of up to $3/kg for hydrogen produced with the lowest lifecycle emissions — a value that seeks to make “green” hydrogen produced from renewable electricity cost-competitive with “gray” hydrogen from fossil fuels in many cases. While Washington State has among the lowest electricity rates in the nation, hydrogen production is still not cost competitive. This additional support could accelerate green hydrogen production to compete economically with fossil fuels for transportation and other end-uses.
In light of these policy and market drivers, leveraging the Pacific Northwest’s ample clean electricity resources to produce “green” hydrogen is a generational economic opportunity that could help provide the region’s aviation, heavy-duty trucking, maritime transport, and industrial companies with the zero-carbon fuels they need to drive down emissions, enhance energy security, and establish the region hub of energy innovation. The Pacific Northwest Hydrogen Association (PNWH2), with support from Washington State’s Consortium for Hydrogen and Renewably-Generated E-Fuels (CHARGE), an initiative of JCDREAM, has assembled regional stakeholders in a proposal for the DOE H2Hub program, and major private-sector developers have already planned their own hydrogen-production investments in Washington. Businesses and governments in the region are already moving to take advantage of this emerging opportunity, demonstrating hydrogen’s potential for zero-carbon trucking, maritime, and aviation fuels.
Jump to a section of the report
As discussed in “Securing Critical Minerals for Washington State”, critical minerals have emerged as a key supply chain concern for project developers as well as policymakers in recent years, owing to the centrality of minerals to clean energy technologies and rising geopolitical tensions with China — a country that controls or has influence over a range of critical mineral inputs. While supply chains for lithium-ion batteries have been perhaps the most notable flashpoint for these concerns, green hydrogen development is also threatened by critical minerals shortages. Various minerals used in zero-emission generation technologies, and especially the platinum and iridium, are required for hydrogen-producing electrolyzers, as well as the platinum used in hydrogen-consuming fuel cells.
This analysis, produced by FP Analytics with support from JCDREAM, identifies the key critical mineral risks throughout the green hydrogen value chain, from zero-carbon electricity generation to hydrogen production to hydrogen end-uses. This project, which accounts for the supply chain requirements and potential risks, is intended to inform the public and interested stakeholders and help inform the region’s long-term hydrogen development strategy.
Expanding the Region’s Zero-Emission Electricity Supplies
The long-term economics of green hydrogen are premised on the availability of low-cost zero-carbon energy resources, which account for 50 percent to 70 percent of levelized hydrogen production costs. In this respect, the Pacific Northwest is well-positioned; 58 percent of Washington and Oregon’s combined electricity generation is from hydropower, with another 11 percent from wind, 5 percent from nuclear, and 1 percent from solar. Powering three-quarters of the region’s electricity needs with existing low-cost clean energy resources gives the region a tremendous advantage in potential green hydrogen lifecycle emissions as well as production costs. As of this writing, rates for industrial electricity users were just 6.06 cents/kWh in Washington and 6.36 cents/kWh in Oregon — two of the three lowest industrial rates in the country, with neighboring Idaho ranked in-between at 6.27 cents/kWh.
DATA SOURCES: U.S. Department of Energy, Energy Information Administration, 2021 State Electricity Profiles
Of course, if the diversion of this zero-carbon electricity for green hydrogen production results in fossil fuel power plants increasing generation to supply a greater share of electricity for other end-uses, the net climate benefits of this transition would be substantially lower. This tradeoff isn’t just a theoretical question and could impact the eligibility of regional hydrogen projects for federal incentives, with significant implications for their overall economics. DOE is currently developing a Clean Hydrogen Production Standard (CHPS) that aims to quantify the lifecycle emission benefits of hydrogen production, which could potentially evaluate monthly or even hourly matching of clean electricity generation to hydrogen production, regional matching of generation, and the complex question of whether this clean generation is “additional” or whether it cannibalizes existing end-uses. The CHPS will be used to determine the level of tax credits that hydrogen production projects receive under the IRA, and applications for H2Hub funding are required to “demonstrably aid achievement” of the standard.
More broadly, squeezing the remaining fossil fuel power from the region’s grids poses a significant challenge for meeting Oregon’s mandate for a 100 percent zero-emission grid by 2040 and Washington’s mandate for a 100 percent zero-emission grid by 2045. Wind and solar are the most quickly growing sources of power on the grid, but when these variable resources aren’t available — i.e., when the wind stops blowing, and the sun stops shining — the gap is often compensated for with natural gas peaker plants, which can ramp up and down much more quickly than hydro or nuclear plants. This issue is greatly exacerbated during months when wind generation is low — typically starting in the late summer to the early winter in the Northwest – as well as winter months of low solar generation.
Eliminating this persistent fraction of fossil fuel use from Washington’s and Oregon’s grids is highly relevant to hydrogen producers, as a challenge for achieving a truly “green” product qualifying for maximum incentives, but also an opportunity to use hydrogen as a long-duration storage medium as discussed below. Getting to a 100 percent zero-carbon grid is also a concern for the growing number of companies prioritizing the purchase of 100 percent clean electricity — including tech giants like Google, Microsoft, and Amazon, which have all made this a goal for their data center operations and have preferentially sited in the region due to its low-cost, low-carbon grid.
Increasing Hydropower Generation
One possibility for increasing zero-carbon energy supplies is adding hydropower and conventional nuclear capacity, building on the baseload foundation of the existing grid. However, opportunities to expand conventional nuclear energy in the region are severely constrained due to the well-documented economic and regulatory obstacles to the development of these facilities. By contrast, while there are inherently limited opportunities to develop new large-scale hydropower dams and growing environmental concerns surrounding some of the region’s existing dams, the DOE’s Hydropower Vision report highlights the potential to develop new hydropower capacity in the region that would have minimal environmental impacts — primarily by upgrading existing hydropower facilities or by adding turbines to existing dams and other water infrastructure such as irrigation canals that do not currently produce power. The economics of the latter opportunities could be boosted by a new DOE loan guarantee program specifically targeting projects that leverage existing infrastructure, which is being considered by developers working on projects to power existing dams in the Pacific Northwest.
Increasing hydropower generation could leverage the region’s plentiful rainfall and existing infrastructure, and its development is minimally dependent on critical minerals. The only mineral supply chain of concern for hydropower is copper, which is used in hydropower turbine windings and has become a source of broader concern due to projected increases in demand that could far outstrip supply expansion. While copper is not included on the USGS list of critical minerals due to its current diversity of suppliers, there have been growing calls from policymakers and analysts to consider its inclusion, particularly in the wake of growing political unrest in Peru (a major copper producer). At the same time, copper is essential to virtually all clean electricity supply technologies due to its use in turbine windings for technologies like wind and nuclear, as well as the transmission cables required to connect clean energy to the grid (or directly to electrolyzers), making it an overarching concern for the energy transition and not just a hydropower-specific issue.
New Sources of Zero-Carbon Electricity
Looking beyond hydropower expansion, the primary opportunities to increase zero-power generation in the near-to-medium term include wind, solar, and advanced nuclear. The first part of this analysis addresses the main critical mineral supply chain risks for deployment of each of these generation pathways going forward. To summarize:
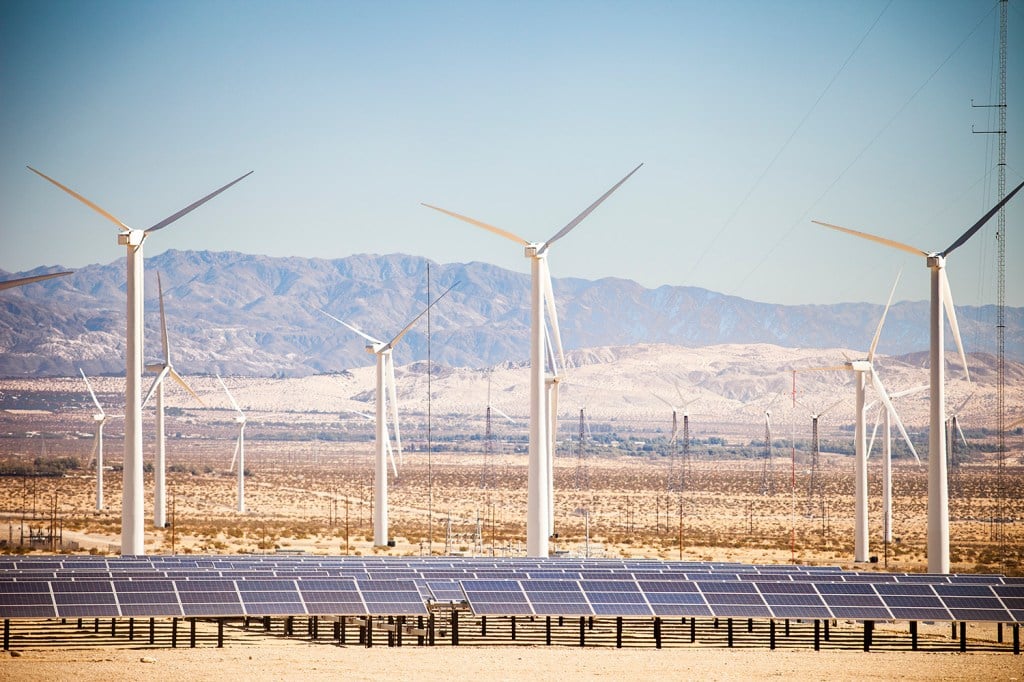
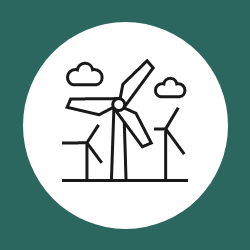
Wind: Direct-drive wind turbines require permanent magnets that use the rare earth elements (REE) neodymium, praseodymium, dysprosium, and terbium, which are a source of major concern due to China’s dominance throughout the supply chain. China is home to 70 percent of the world’s rare earths element (REE) production, 87 percent of its processing, 92 percent of the manufacturing of permanent magnets, and 58 percent of wind turbine manufacturing. The lower maintenance costs of direct drive turbines make them particularly essential for offshore wind, where they account for over three-quarters of U.S. installations. While the Pacific coast has no offshore wind currently, due to its steeply sloping continental shelf, the commercialization of floating offshore wind is driving a flurry of new interest, including projects proposed off the coasts of Oregon and Washington. For onshore wind installations, including current and many future projects in the region, direct-drive turbines are less necessary. However, China is home to nearly half of the manufacturing capacity for gearboxes these turbines require, posing another potential supply chain risk (albeit not one involving critical minerals).
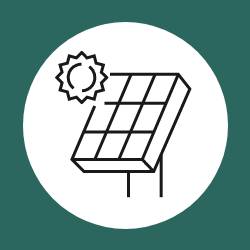
Solar: While solar represents just 1 percent of Oregon and Washington’s current generation mix, in large part due to the region’s relatively poor solar resource, there is growing interest in developing new utility-scale projects in sunnier regions to the east in both states. Solar faces similar tradeoffs as wind, however. On one hand, the manufacturing supply chains for conventional crystalline silicon photovoltaic (PV) cells is dominated by China, and the production of polysilicon in the Xinjiang region — where the oppressed Uyghur population is often used as forced labor — has triggered a crackdown on Chinese imports by U.S. lawmakers. On the other hand, the thin-film solar panels produced by U.S.-based First Solar are less suited for generation in the cloudy Pacific Northwest and moreover depend on supplies of cadmium and tellurium — critical minerals that are primarily produced in China.
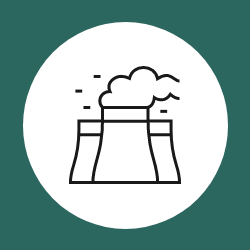
Advanced nuclear: The Pacific Northwest has emerged as an early leader in the development of advanced nuclear technologies, which have the potential to reduce costs and development timelines compared to conventional nuclear, thanks to modular, factory-produced designs. Terrapower, a Bill Gates–founded startup based in Washington, and X-Energy, a Maryland-based company planning its first project in Washington with Energy Northwest, were both selected for up to $3.2 billion in grants by the U.S. Advanced Reactor Demonstration Program. However, these and many other advanced nuclear startups will depend on HALEU (high-assay low-enriched uranium) fuels, which are currently only commercially available from a Russian company, posing a clear supply chain challenge. Terrapower has already warned that the operations at its first project could be delayed by up to two years from its originally planned 2028 start date while secure HALEU supply chains are developed.
Beyond these advanced nuclear fission approaches, nuclear fusion would eliminate the requirement for enriched uranium fuel altogether, instead using potentially limitless isotopes of hydrogen such as deuterium and tritium. Washington is home to several fusion startups, including Helion Energy, Zap Energy, CTFusion and Avalanche Energy, with the most ambitious aiming for commercial deployments by the early 2030s — just a few years behind the timelines for advanced nuclear. However, nuclear fusion is fundamentally less proven on a technical level than nuclear fission and is thus unlikely to play a role in near-term plans for hydrogen hubs or to be deployed in time to receive hydrogen tax credits under the IRA.
A Growing Range of New (and Old) Energy Storage Technologies
Energy-storage technologies offer a third, and potentially very promising, pathway to squeeze out these last fossil fuels from the region’s grids, allowing for excess zero-carbon generation from wind and solar at times of lower demand to be “saved” for meeting demand peaks, instead of relying on fossil fuels. Compared to the high-density energy storage required for EVs, the relative lack of space constraints for grid-scale installations opens up opportunities for a greater variety of technology options, with different combinations of duration, cost, and supply chain risks. The Pacific Northwest National Laboratory (PNNL) produces comprehensive cost and performance estimates for a wide range of emerging and established storage technologies, including several suited for near-term deployment as part of hydrogen hub developments in the region.
DATA SOURCES: Pacific Northwest National Laboratory, 2022 Grid Energy Storage Technology Cost and Performance Assessment, LCOS Estimates
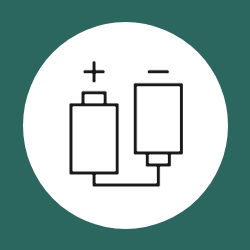
Lithium-ion Batteries: The same types of lithium-ion batteries used in EVs can be aggregated into large, grid-scale storage facilities, which is often the lowest-cost solution for managing generation on an hourly basis but may be insufficient for weeks of low wind or winter months of lower solar availability. Lithium-ion batteries typically have durations of four hours, and while augmenting installations with additional capacity can mitigate this limitation to some extent, the economics of lithium-ion grid storage rapidly worsen for use cases of ten hours or more.
The highest-performing lithium-ion batteries that are typically used in EVs, known as nickel manganese cobalt (NMC) batteries, rely on several critical minerals with significant supply chain risks, including lithium, cobalt, nickel, and graphite. While China mines little or no lithium, cobalt, and nickel domestically, it has invested heavily in mining operations in leading producers, including Chile (for lithium), Congo (for cobalt), and Indonesia (for nickel). Perhaps more importantly, China dominates midstream processing, including a 65 percent share of cobalt processing, 58 percent of lithium processing, and 35 percent of nickel processing. It also produces over 65 percent of the world’s natural graphite and processes almost all of the spherical graphite required in battery anodes.
Given mounting concerns surrounding cobalt and nickel in particular, there has been growing interest in lithium iron phosphate (LFP) batteries, an older lithium-ion chemistry that suffers from reduced energy density but also replaces nickel and cobalt in the cathode with earth-abundant iron phosphate, reducing costs and easing critical mineral supply chain concerns. LFP batteries are thus relatively well suited for grid storage installations where size and weight are less of a concern than vehicles, although automakers are also increasingly turning toward them for smaller, lower-range EVs. Still, China controls or influences over 75 percent of the world’s lithium-ion battery manufacturing capacity, including both NMC and LFP.
While the BIL and IRA are catalyzing a wave of U.S. battery manufacturing and supply chain investments, much or all of the planned output in most cases will be preferentially sold to automakers for EV production, either through exclusive arrangements and joint ventures or simply because of the much higher demand the EV segment represents. Thus, grid storage projects may struggle in some cases to secure supplies from new domestic producers, or else they may have to pay a premium compared to high-volume EV manufacturers.
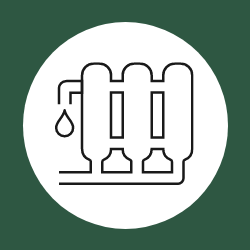
Redox Flow Batteries: Flow batteries represent an alternative battery architecture that is well suited to grid storage applications, offering a commercially mature technology with a cost of storage that can be broadly similar to lithium-ion for most applications — although, like lithium-ion batteries, their economics suffer dramatically beyond ten-hour durations. Redox flow batteries (RFBs) pump liquid electrolytes between storage tanks separated by a membrane into anode and cathode compartments, passing through electrodes and charging or discharging electricity as required. This design offers longer lifespans than lithium-ion batteries, storage durations of ten hours, and flexibility in design to meet specific grid needs; the power (MW) of a system can be increased by adding more cells, and the capacity (MWh) can be increased by increasing the quantity of electrolyte.
RFB supply chains are less well developed than lithium-ion batteries, due to the much smaller size of the market, but this limitation is mitigated to some extent due to the fact that grid storage developers do not have to compete for supplies with automakers. The technology has other supply chain security advantages over lithium-ion batteries as well, as most RFB components are simple pumps, tanks, and electrolyte chemicals that are easy to source, and the U.S. is home to a number of flow battery manufacturers. One drawback is that the most established RFB battery chemistry uses vanadium, a critical mineral that is mined primarily in China and Russia, although U.S. manufacturers source most of their processed vanadium chemicals from South Africa and Brazil. While PNNL only provides estimates of vanadium RFBs, other companies use less-established chemistries, including iron, zinc, or other materials.
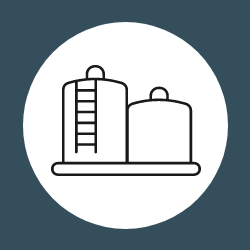
Pumped Storage Hydropower: Like hydropower in relation to other forms of renewable energy, pumped storage hydropower (PSH) is the oldest and most widespread form of grid-scale energy storage, currently accounting for 93 percent of utility-scale storage in the U.S. and 97 percent of utility-scale storage capacity in Washington and Oregon combined. Crucially, it is also one of the most economic long-duration energy storage (LDES) technologies and by far the most proven, maintaining low costs for all durations above four hours modeled by PNNL.
Pumped hydro storage installations use electricity to pump water from a lower reservoir to a higher one during times of excess electricity supply, which is then used to generate hydropower during times of peak demand. Typically, PSH facilities are connected to existing, dammed bodies of water, often in conjunction with existing hydropower plants. While opportunities to develop traditional PSH are geographically and hydrologically limited in a similar way to hydropower, there remains significant unexploited potential for development at existing dams.
Perhaps more promisingly, “closed-loop” PSH designs have been developed that eliminate the need for a connection to existing bodies of water, instead using two engineered reservoirs. By avoiding environmental concerns associated with disturbing natural rivers, this innovation could significantly expand opportunities to develop PSH, especially in regions such as the Pacific Northwest, where water supplies are plentiful. One of the first such facilities being developed in the U.S. is the proposed 400 MW Swan Lake Energy Storage Project in Klamath County, Oregon, and another early-stage project on the Washington-Oregon border could add an additional 1.2 GW of closed-loop pumped hydro storage.
Overall, DOE’s Hydropower Vision report estimates that the U.S. could nearly double its existing PSH capacity by 2030, primarily through upgrades to existing facilities as well as the development of new facilities at existing dams, including a significant amount in the Pacific Northwest. Like hydropower plants, their construction does not depend on critical minerals, although copper is required for the turbine windings.
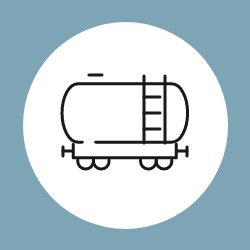
Hydrogen: The other promising and relatively proven LDES technology option for the Pacific Northwest is the use of hydrogen itself as a storage medium. Green hydrogen can be generated from excess wind and solar and then stored for months at a time in tanks or underground caverns, much like natural gas, allowing it to be converted back into electricity using fuel cells or modified gas turbines, as discussed in detail in the following sections. PNNL’s modeling is based on polymer electrolyte membrane (PEM) fuel cells, since it is a more established hydrogen generation technology and indicates potential storage costs for durations of ten hours or more that are dramatically lower than batteries, albeit significantly higher than PSH. Several manufacturers are testing modifications to gas turbines that would allow for the direct combustion of hydrogen, including a joint development agreement for hydrogen turbine testing between Puget Sound Energy and Mitsubishi, but the higher temperatures and risk of corrosion from burning pure hydrogen may require special alloys or coatings using critical minerals such as yttrium and chromium.
Also as discussed below, PEM electolyzers and fuel cells have critical mineral risks, albeit of a different profile from that of batteries, with the primary concerns surrounding platinum and iridium. Of course, any hydrogen hub using PEM electrolyzers — the most likely choice for ramping up and down to match renewable generation and minimize emissions, in line with CHPS requirements — will face these risks, meaning the additional use of hydrogen as a storage medium only adds incremental risk for additional quantities of critical minerals. Moreover, hydrogen storage offers much greater flexibility in deployment than PSH and can be deployed in conjunction with an integrated hydrogen hub design, making this a particularly appealing LDES option.
Hydrogen Electrolyzer Technologies
Electrolyzers are the core technology for green hydrogen production, converting water and electricity into hydrogen and oxygen. While there are several different types of electrolyzers, they all consist of “stacks” of an anode and a cathode separated by an electrolyte, with the main structural differences being different types of electrolyte material. Washington is already home to one of the largest electrolyzer installations in the country, a deployment of Cummins electrolyzers by the Douglas County Public Utility District at Wells Dam in 2020 that generates hydrogen during times of excess wind generation instead of ramping down hydropower generation. Australia’s Fortescue Future Industries (FFI) and the U.S.-based international energy company Invenergy are also planning much larger-scale installations in Washington.
DATA SOURCES: BloombergNEF, “A Breakneck Growth Pivot Nears for Green Hydrogen”
The three main types of electrolyzers that are currently available include alkaline electrolyzers, proton exchange electrolyzers, and solid oxide electrolyzers, each of which offers different combinations of cost, performance, and supply chain and critical minerals risks.
Alkaline electrolyzers
Supply chain risks: Alkaline electrolyzers have the longest track record, lowest costs, and largest scale, but are poorly suited to ramping up and down with variable renewables. China dominates their manufacturing as well as mineral supply chains.
Click each mineral for more
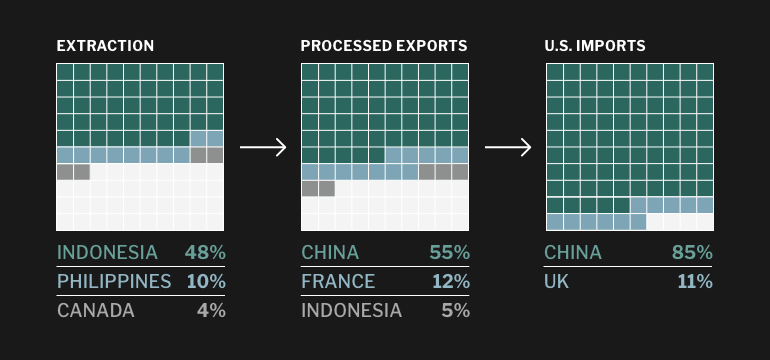
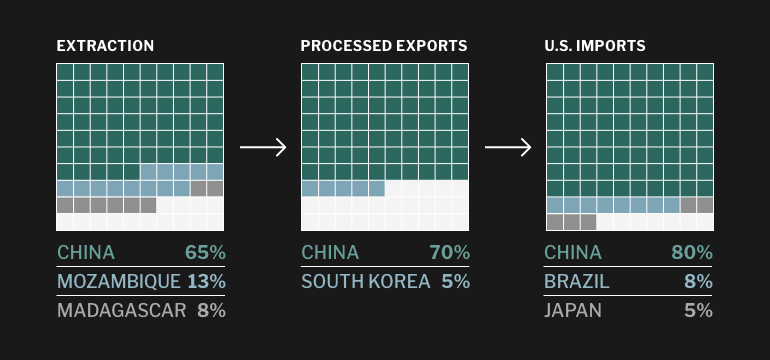
DATA SOURCES: US DEPARTMENT OF ENERGY; WORLD BANK GROUP AND THE HYDROGEN COUNCIL
Alkaline electrolyzers are the oldest type of electrolyzer, having been developed over a century ago. They use a liquid alkaline solution for an electrolyte, typically sodium or potassium hydroxide, which is transported across cathodes made of nickel and graphite, critical minerals that, as noted above, are produced in Indonesia, the Philippines, and China and processed mostly in China. Alkaline electrolyzers account for over 70 percent of current electrolyzer manufacturing capacity, and Chinese firms account for nearly 70 percent of alkaline’s share, which, combined with their critical mineral requirements, make alkaline electrolyzers the hydrogen production pathway with perhaps the highest overall supply chain risk. However, there are a handful of major European manufacturers of alkaline electrolyzers that are expected to grow their share of the market in 2023, and PNWH2 board member Fortescue Future Industries (FFI) has developed its own alkaline electrolyzer and is building an expansive manufacturing facility in its home country of Australia.
Because alkaline electrolyzer stacks are a very mature technology, they typically have the lowest capital costs, although, as discussed below, the total installation cost and hydrogen production costs of PEM electrolyzers are increasingly competitive. Alkaline electrolyzers also have a technical shortcoming with particular relevance to green hydrogen producers that are striving to minimize their emissions profile, however: they perform best when operating constantly, at a steady state, and are slow and inefficient when ramping up and down in response to changing electricity supplies. For green hydrogen producers that are seeking to utilize variable wind and solar resources for some or all of their electricity inputs, this is a major drawback.
PEM Electrolyzers
Supply chain risks: PEM electrolyzers are an established technology that is more well-suited to producing hydrogen from renewables, and leading manufacturers in the US and Europe are rapidly scaling up production. They have a variety of critical minerals requirements, with platinum and especially iridium most prominent due to concentration in South Africa and scarcity of iridium in particular.
Click each mineral for more
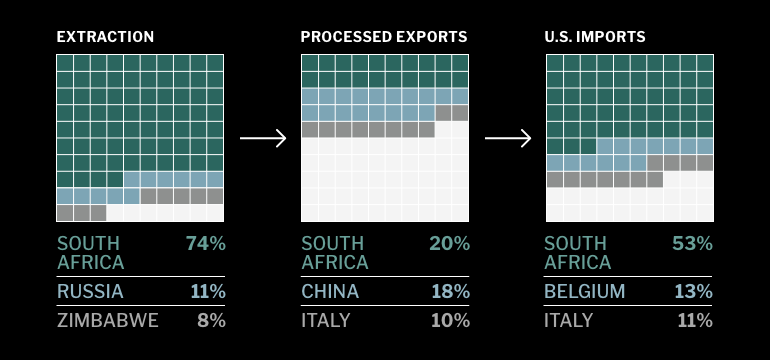
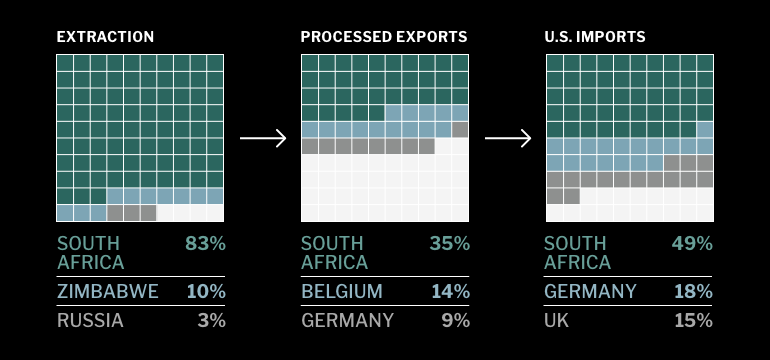
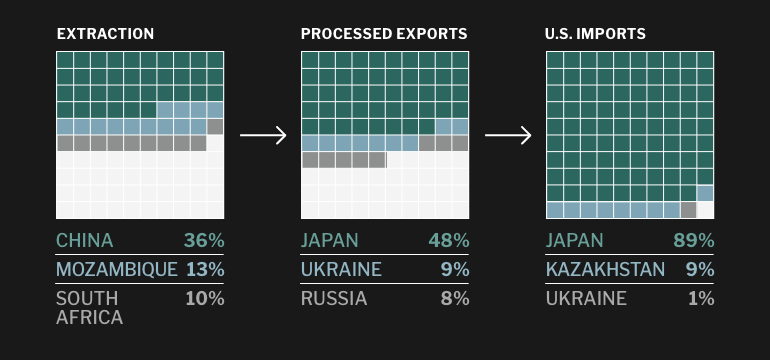
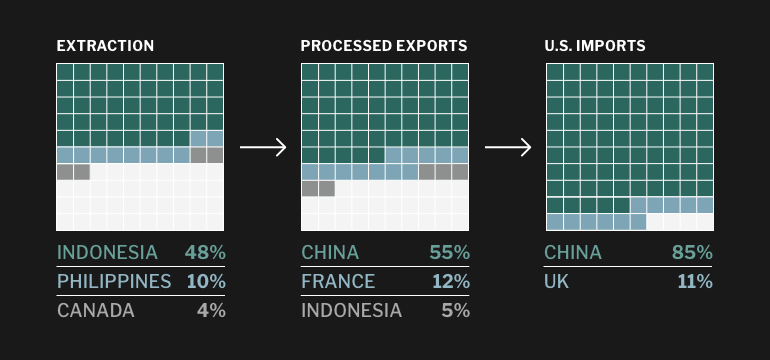
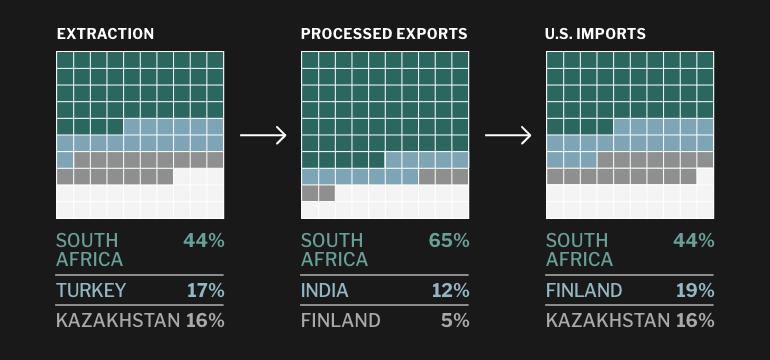
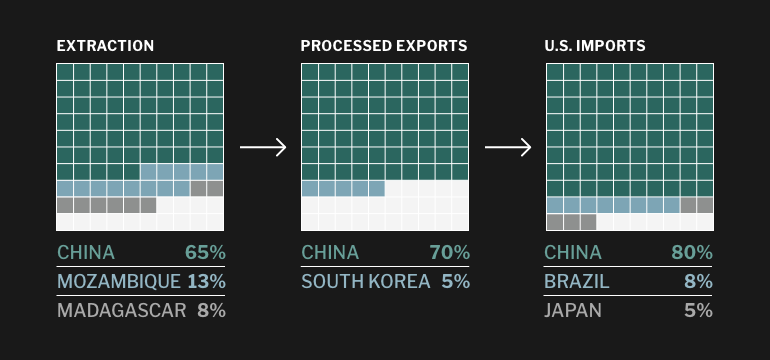
DATA SOURCES: US DEPARTMENT OF ENERGY; WORLD BANK GROUP AND THE HYDROGEN COUNCIL
PEM electrolyzers utilize a solid plastic membrane material for an electrolyte, which selectively allows positively charged hydrogen ions to move from the anode to the cathode, where they combine with electrons from electricity inputs to form hydrogen gas. They have been a focus for U.S. and EU hydrogen developers due to notable performance advantages over alkaline electrolyzers, including the ability to ramp up and down quickly and efficiently with electricity availability, which makes them ideally suited for matching variable renewable generation. They also require significantly less space, with U.S. manufacturer Plug Power estimating a two- to three-times smaller footprint for its systems, compared to alkaline alternatives. While PEM electrolyzers are a newer technology than alkaline, they have been fully commercialized, with deployments including the Wells Dam installation referenced above.
PEM electrolyzers are also considered increasingly cost-competitive with alkaline, with research cited by Plug Power showing potentially lower total cost of ownership for large-scale facilities in particular due to lower balance-of-plant requirements as well as lower maintenance costs, compared to alkaline electrolyzers. Moreover, Platts estimates that combined incentives for renewable electricity generation and new IRA incentives for green hydrogen production could potentially result in near-zero hydrogen costs in areas with low electricity prices, with further declines in cost as manufacturing scales up.
In terms of manufacturing supply chains, PEM electrolyzers offer a stark contrast to alkaline’s China-dominated production; U.S. firms account for over 60 percent of current PEM manufacturing capacity, with leading companies including Plug Power, Cummins, and Ohmium (which manufactures its electrolyzers in India), and the EU and UK accounting for another 33 percent. According to Bloomberg NEF, this overwhelming market share in PEM will be maintained as the industry scales up in the years ahead, with total PEM manufacturing capacity expected to more than double in 2023, and the U.S. and EU continuing to account for over 95 percent of the total.
However, PEM electrolyzers have significant critical mineral supply chain concerns, which may increase in the years ahead. Their manufacture typically requires critical minerals for several components, including:
- Titanium, used in coatings for bipolar plates, is mined in China, South Africa, and Brazil and imported in refined forms from Japan.
- Nickel and chromium alloys are used in bipolar plates, gas diffusion layers, and end plates. Chromium and ferro-chromium used in alloys is primarily mined and imported from South Africa, while nickel mining is led by Indonesia and the Philippines, with refined metallurgical-grade oxides imported mostly from China.
- Graphite, used in catalyst supports as well as carbon fiber end plates, is mined in natural forms, refined, and imported overwhelmingly from China.
However, the most pressing critical mineral concern for PEM electrolyzers are the platinum group metal (PGM) catalysts that drive the splitting of water into hydrogen and oxygen, with a cathode made of platinum and an anode that uses iridium. Nearly three-quarters of the world’s platinum is mined and processed in South Africa, a historically stable trading partner, with production and refining primarily by large, publicly traded companies (Anglo American, Implats, Sibanye-Stillwater, and Northam Platinum). Iridium is produced almost exclusively as a byproduct of platinum, and a rare one at that — it accounts for just 2 percent of world PGM mining production, the lowest share of any PGM, and the U.S. is 100 percent reliant on imports, primarily from South Africa.
Such a heavy concentration of production in one country poses inherent risks, and South Africa’s production has suffered in the past due to worker strikes, social unrest in the regions where these mines are located, and accidents. Perhaps most concerning in recent years has been a deepening electricity crisis on the aging, state-owned (and largely coal-powered) electricity grid, with recent blackouts reaching over 11 hours a day, leading to a declaration of a national disaster. These outages were a primary reason why PGM production dropped by an estimated 6 percent in 2022, compared to expectations, with one of the world’s leading producers, Anglo American Platinum, cutting production by 37 percent over the last three months of the year. Analysts have warned that production could drop further in the years ahead absent a solution, although Anglo American and other miners are looking to develop their own solar and battery resources to boost their resilience.
South Africa is also virtually certain to remain an indispensable, central player in global platinum supply chains over the long term, with 90 percent of global PGM reserves. The second- and third-largest producers of platinum are Russia and Zimbabwe, with 11 percent and 8 percent of production, respectively, but each poses clear political risks to supply chain reliability. The U.S. itself produces 2 percent, and Canada produces another 3 percent, but these mines are both owned by South African companies, which ship PGM ores back to South Africa for separation and refining.
The U.S. derives roughly eight times as much platinum from recycling catalytic converters — one of the main drivers of global platinum production, accounting for 40 percent of consumption — as it does from its own mines, but it remains nearly 80 percent dependent on imports.
In its evaluation of global sufficiency of critical mineral supply chains for hydrogen production and consumption, the World Bank found that projected increases in primary iridium and platinum demand through 2050 are by far the greatest of any mineral. Primary platinum demand is projected to increase by between 10 percent and 30 percent, compared to current levels of production, driven by demand for both electrolyzers and fuel cells — particularly fuel cells for heavy-duty trucks, which are expected to drive the majority of demand.
This demand increase is projected to peak at over a third of current production levels in the 2030s, and then subsequently fall and level off in the 2040s due to expected reductions in the platinum intensity of electrolyzer designs as well as rising availability of recycled platinum from within the sector. Reduced demand for catalytic converters as ICE vehicles are increasingly phased out should also provide a boost to available scrap as well as mitigate risks to supplies in the long term, although it also represents a risk if the pace of hydrogen-driven demand increases lag behind the pace of ICE phaseouts, reducing incentives to maintain investments in platinum mining.
Meeting iridium demand represents a steeper, as well as thornier, challenge. The World Bank scenarios project iridium demand for hydrogen electrolyzers in 2050 to amount to between 35 percent and 90 percent of current primary production levels, more than double the expected relative increase of platinum demand. Moreover, because it is a byproduct, the production of iridium is essentially only responsive to overall platinum production, although unresponsiveness to demand could be partially mitigated if rising iridium prices increase efforts to extract it from PGM ore. This issue is exacerbated by the fact that a typical PEM electrolyzer requires over 70 percent more iridium than platinum per megawatt of capacity, posing a fundamental imbalance that could be the most significant and acute constraint on manufacturing as the hydrogen market grows.
A combination of advances in two areas will almost certainly be needed to ensure that bottlenecks in iridium supplies do not create major disruptions in the scaling-up of PEM electrolyzers. First, it will be essential to reduce the iridium loading requirements for electrolyzers; the World Bank projections assume a reduction in iridium requirements of 80 percent by 2050, and this goal is being pursued by both startups and government researchers. The other key variable is the degree to which iridium is recycled, from electrolyzers and other uses, such as certain types of spark plugs, which currently have low recovery rates and have potential for significant increases in supplies as ICE vehicles are phased out. More generally, the recycling of both platinum and iridium from fuel cells could likely leverage approaches and infrastructure used in the well-established PGM recycling ecosystem.
Solid Oxide Electrolyzers
Supply chain risks: Solid oxide electrolyzers are still at an early stage of scaling up, but they are commercially available, with leading producers in the US and EU. They are particularly well-suited for generating hydrogen from nuclear power because of their ability to harness waste heat to boost efficiency, but also require a variety of critical minerals including rare earth elements sourced almost entirely from China.
Click each mineral for more
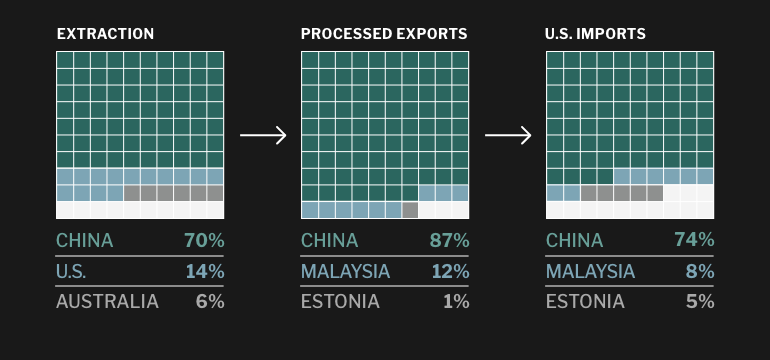
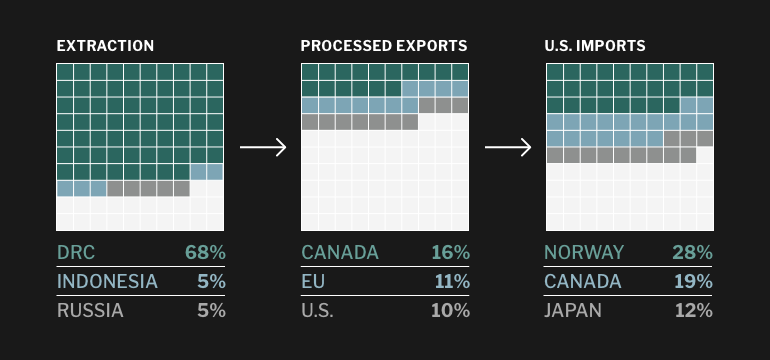
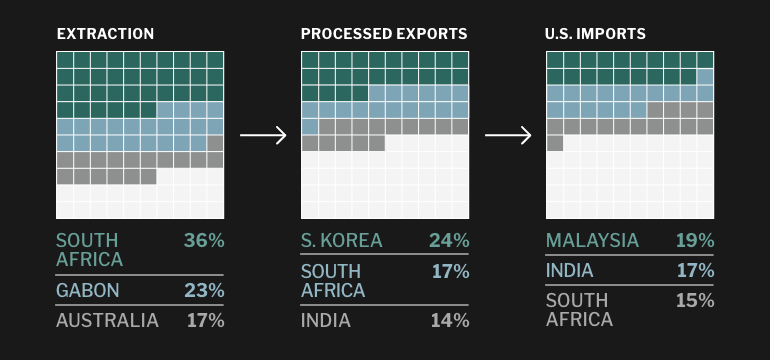
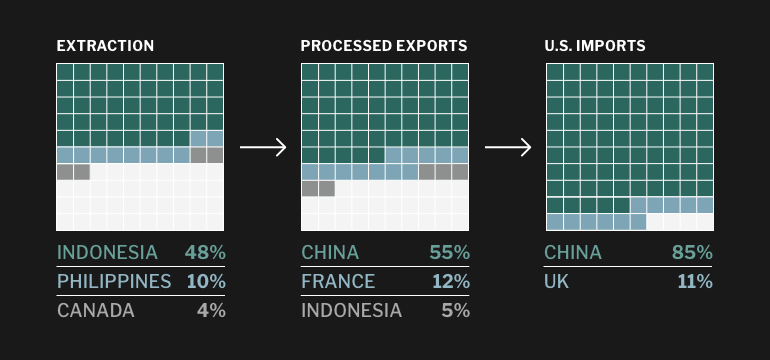
DATA SOURCES: US DEPARTMENT OF ENERGY; WORLD BANK GROUP AND THE HYDROGEN COUNCIL
Compared to alkaline and PEM electrolyzers, solid oxide electrolyzer technology, manufacturing capacity, and supply chains are less developed, with a TRL (technology readiness level) of 7, compared to 9 for alkaline and PEM. However, a growing number of U.S, European, and Japanese manufacturers are beginning to commercialize them, and they offer unique performance benefits as well as critical mineral requirements. Solid oxide electrolyzers use a solid ceramic electrolyte material that requires temperatures of 700° to 800°C to function, and they produce hydrogen from steam instead of liquid water. This process gives solid oxide electrolyzers a natural affinity for pairing with nuclear plants, as they produce waste heat that can be used to reduce electricity inputs (and thus the operating costs) required to achieve these temperatures. The high operating temperatures of solid oxide electrolyzers can also be paired with the production of ammonia, methanol and other synthetic fuels, steel, and other materials. Solid oxide electrolyzers have thus emerged as a focus for demonstrations of nuclear-powered electrolysis for DOE as well as the private sector, including the partnership between NuScale and Shell.
Similar to PEM electrolyzers, the U.S. is one of the leaders in the development of this emerging technology and is competitive throughout the manufacturing supply chain, from components to finished stacks and systems. Solid oxide electrolyzers also require a greater variety of critical minerals than alkaline or PEM electrolyzers, including:
- Yttrium, a key ingredient used to create the ceramic electrolyte, is a rare earth element mined and imported almost exclusively from China.
- Lanthanum, cobalt, and manganese are used in the solid air electrodes. Lanthanum is a rare earth element; its mining, processing, and exports are dominated by China. Cobalt is primarily produced in Congo and processed into metallic form for export in China, Finland, and Belgium. Manganese is mined in South Africa, Gabon, and Australia, and imported in refined ferromanganese form from Malaysia, South Africa, and India.
- Nickel, used in the solid fuel electrode, is mined mostly in Indonesia, the Philippines, and Canada, with China and Indonesia leading in refining capacity, and U.S. imports coming chiefly from China.
Anion Exchange Membrane Electrolyzers
Supply chain risks: AEM electrolyzers are at a precommercial stage of development, but interest in this technology is growing due to its potential to combine PEM-like performance with reduced critical minerals requirements. AEM electrolyzers use relatively earth-abundant nickel-iron alloy catalysts, although some researchers are exploring potential performance benefits from adding cobalt or other critical minerals.
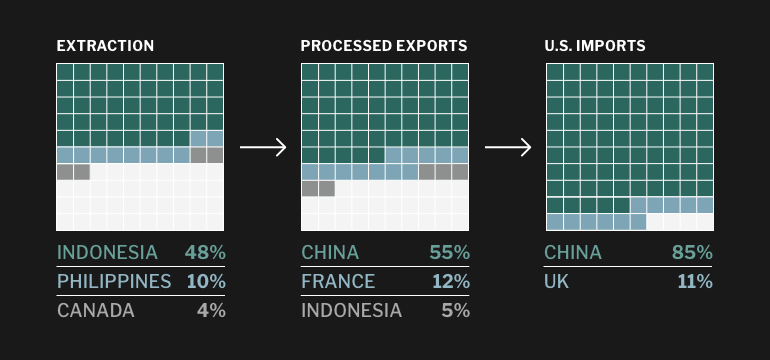
DATA SOURCES: US DEPARTMENT OF ENERGY; WORLD BANK GROUP AND THE HYDROGEN COUNCIL
One lesser-developed but promising type of electrolysis technology is the anion exchange membrane (AEM) electrolyzer, which seeks to combine the advantages of alkaline and PEM electrolyzers. Like PEM electrolyzers, AEM electrolyzers use a solid polymer electrolyte that allows for rapid ramping up and down in response to variable renewable electricity inputs. However, similar to alkaline electrolyzers, they operate in a mild alkaline environment, which avoids the need for the expensive platinum-group catalyst materials and titanium bipolar plates required to survive in the acidic conditions of PEM electrolysis. In their place, AEM electrolyzers may use nickel-iron catalysts and steel bipolar plates, significantly lowering materials costs as well as reducing (if not eliminating) critical mineral supply chain risks.
While AEM electrolyzers are at an earlier stage of development, growing interest in hydrogen is leading to rapid improvements. In 2020, researchers at Washington State University and Los Alamos National Laboratory demonstrated AEM performance at comparable levels to PEM electrolyzers, although they noted that the durability of these prototypes remains limited. Other researchers have explored the potential for the addition of critical minerals including cobalt, platinum, or ruthenium (another PGM) to improve performance. Given accelerating research into this technology, the IEA revised its assessment of AEM technology from TRL4 (early prototype stage) to TRL6 (full prototypes at scale) in 2022, and noted that the German company Enapter is aiming to scale up mass production of its modular AEM electrolyzers in 2023.
Connective Infrastructure
One critical concern for developing a hydrogen hub is what the H2Hub program calls “connective infrastructure,” which encompasses all of the equipment from hydrogen production to end uses. This includes the infrastructure required to transport hydrogen from electrolyzers to end-use sites, store it in sufficient quantities, and, if applicable, dispense it to vehicles. For all of these segments, hydrogen projects typically leverage established technologies originally developed for natural gas applications, albeit with modifications required to handle hydrogen’s different characteristics, including lower density, higher requirements for compression, and its tendency to degrade the fatigue and fracture resistance of materials, known as “hydrogen embrittlement.”
The timely development of this infrastructure is essential to the success of a hydrogen hub, its components are not dependent on critical mineral supply chains, largely relying on stainless steel and other relatively abundant materials.
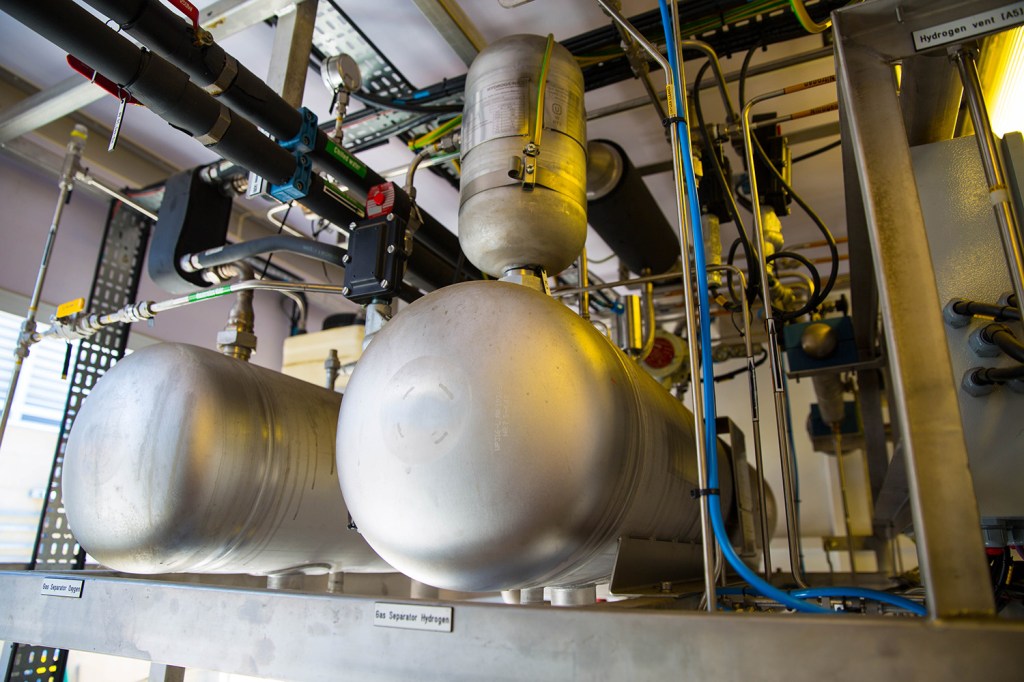
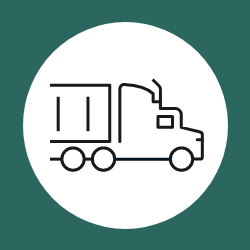
Transportation: Overland hydrogen transportation is typically done via pipelines or tube trailers in gaseous or cryogenically liquefied form, with pipelines having higher up-front capital costs but superior overall economics for moving large volumes of hydrogen. There are over 1,600 miles of hydrogen pipelines already operating in the U.S., 90 percent of which are located around oil refineries and chemical plants in the Gulf Coast region. While hydrogen pipelines are broadly similar to natural gas pipelines, and in some cases can potentially be converted from existing natural gas pipelines, they require modifications to compressors, valves, seals, leak-detection systems, and other components, and only certain grades of steel can be used to avoid embrittlement and cracking.
Currently, X42, X52, and X60 grades of carbon steel are being used in hydrogen networks, and these alloys primarily rely on manganese, a critical mineral, along with carbon, sulfur, and phosphorus. Smaller amounts of other critical minerals, including niobium, titanium, vanadium, nickel, and/or chromium may be included as well. As an alternative to steel, fiber-reinforced polymer (FRP) has potential as an option for hydrogen pipeline material, which DOE estimates could reduce installation costs by 20 percent.
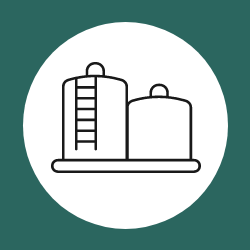
Storage: Pressurized hydrogen storage tanks, for both tube trailers and on-site storage, are typically made from steel as well. As with natural gas, however, the most cost-effective solutions for large-scale bulk storage of hydrogen are underground storage facilities. Options are generally determined by regional geological conditions and cycling requirements, with potential options for storage in salt caverns, saline aquifers, lined hard-rock caverns, and depleted oil and gas reservoirs. While depleted oil and gas reservoirs and saline aquifers are abundant and account for roughly 90 percent of existing natural gas storage capacity, their porosity makes them less flexible and able to cycle only a few times per year. Salt caverns offer more frequent cycling but are relatively rare geologically. Lined hard-rock caverns are the most expensive to develop but offer the fastest cycling and greatest geographic flexibility, making them likely the most broadly applicable option for colocation with a hydrogen hub.
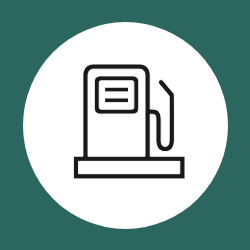
Dispensing: Hydrogen-fueled transportation, a core focus for hydrogen hubs in the region, requires refueling stations as a final component in connective infrastructure. There are currently 56 hydrogen refueling stations operating in the U.S, all of which are located in California. While hydrogen refueling infrastructure is broadly similar to that used for compressed natural gas vehicles, the higher pressures required to manage hydrogen’s lower energy density requires more powerful compressors as well as higher-pressure storage tanks, especially for heavy-duty trucks, aviation, and maritime transportation options that require more fuel. Achieving high-throughput flow rates for rapid fueling of 700-bar onboard storage will require the development of new safety standards, which could take several years.
End-Uses
While competing H2Hub projects will likely draw upon similar hydrogen production technologies and connective infrastructure options, hydrogen has an incredibly diverse set of potential end-uses, spanning virtually every segment of the energy and transportation industry as well as industrial applications, such as steelmaking and chemical manufacturing. It can be used as a feedstock for ammonia production and fertilizers, industrial semiconductor production, steel manufacturing, among other applications. As discussed above, the Pacific Northwest has a unique opportunity to demonstrate hydrogen’s potential to help eliminate remaining fossil fuel consumption on a high-renewables grid, but it also offers exceptional opportunities to demonstrate hydrogen’s utility for a range of end-use applications. While battery-based EVs are expected to dominate light-duty passenger vehicles, hydrogen has strong potential for use in heavy-duty trucking, maritime transportation, and aviation due to higher energy density and faster refueling times, both of which are especially important concerns as vehicle size and weight increase. It also will impact agriculture through cleaner fertilizers. As discussed below, the region is home to industry leaders that are already making moves to deploy hydrogen across all of these areas.
DATA SOURCES: INTERNATIONAL ENERGY AGENCY, NET ZERO BY 2050: A ROADMAP FOR THE GLOBAL ENERGY SECTOR
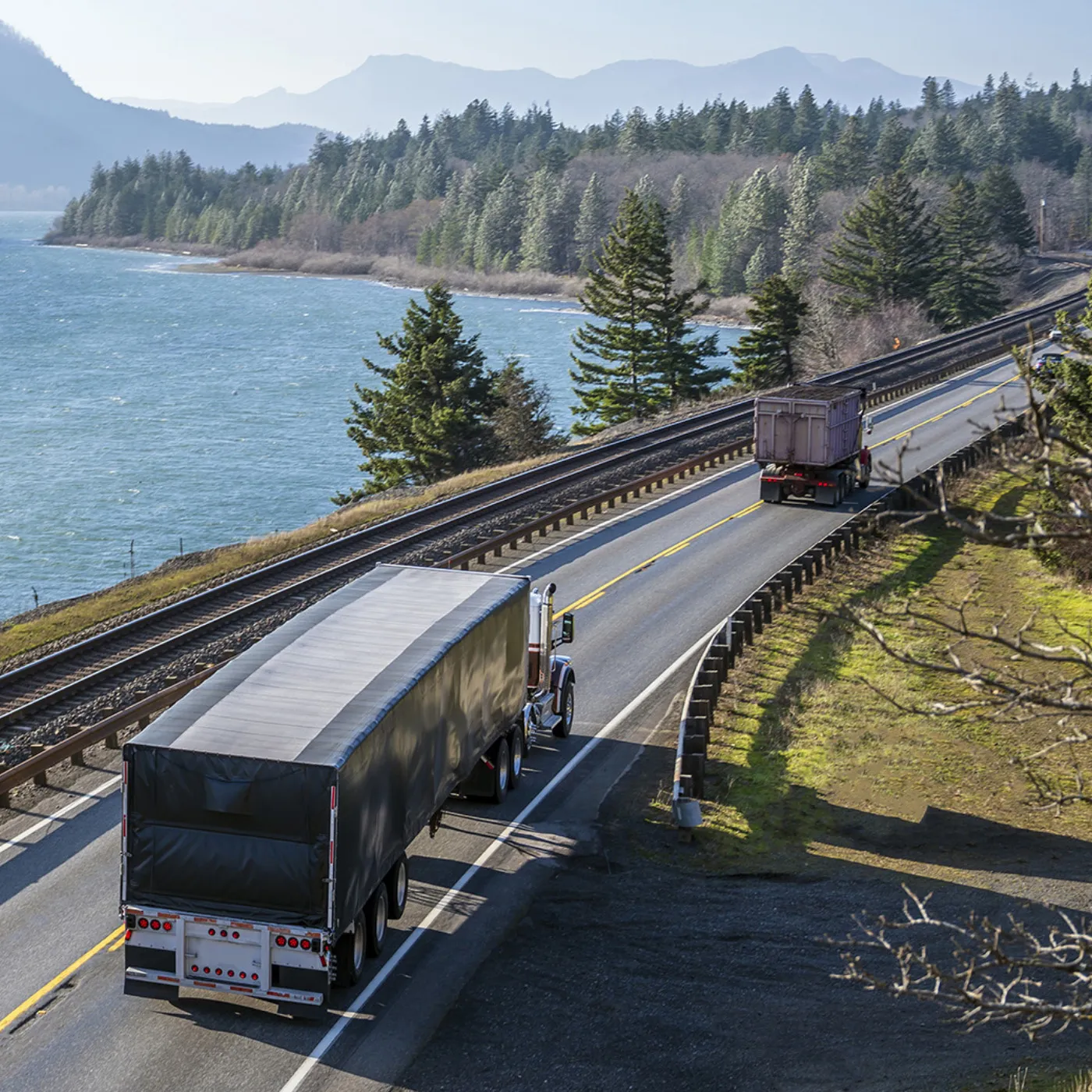
Heavy-duty trucking
Fuel cells have been under development for hydrogen-based transportation for decades, and they are particularly relevant for heavy-duty trucking. They essentially function as electrolyzers in reverse, taking hydrogen fuel and air and converting them to electricity and water using a similar architecture consisting of an anode and a cathode sandwiched around an electrolyte. In contrast to the competition between alkaline and PEM electrolyzers, however, PEM designs have been the clear development focus for transportation end-uses in particular, due to their fast response and greater power density. Like PEM electrolyzers, PEM fuel cells depend on platinum, with all of the attendant supply chain risks described above. However, platinum is used for both the cathode and anode, which eliminates the dependence on iridium supplies that electrolyzers face. To improve durability, fuel cells may also utilize cerium, a rare earth element (REE) that, like other REEs, is produced and processed almost entirely in China, although it is the most abundant of this group.
While fuel cell trucks could face increasingly fierce competition from EV alternatives in years ahead, given ongoing improvements in battery cost and performance, there is a growing base of fuel cell truck manufacturing in the U.S. According to the IEA, ambitious manufacturing scale-up plans by U.S. hydrogen trucking startups Hyzon and Nikola would amount to nearly half of projected global demand in 2030 under an aggressive decarbonization scenario. Toyota has also announced plans to build a manufacturing facility for fuel cells designed for trucks in the U.S., and it recently demonstrated its fuel cells in Class 8 trucks built by Washington-based manufacturer Kenworth (a PACCAR company). Plug Power is another major domestic producer of fuel cells for transportation applications, which are produced at a factory in Spokane.
Fuel cells also have tremendous potential for cleaning up heavily polluting drayage trucks at ports, which are major sources of local air pollution, health risks, and environmental justice concerns for workers and neighboring communities. The Port of Seattle, one of the largest container ports in the country, has announced a partnership with the Pacific Northwest National Laboratory to study the use of hydrogen to power medium- and heavy-duty vehicles, including forklifts, drayage trucks, and cranes, as well as to provide electricity to cargo and cruise ships while they are docked. The Toyota and Kenworth partnership has already proven the potential of this approach with a successful demonstration of fuel cell drayage trucks at the Port of Los Angeles.
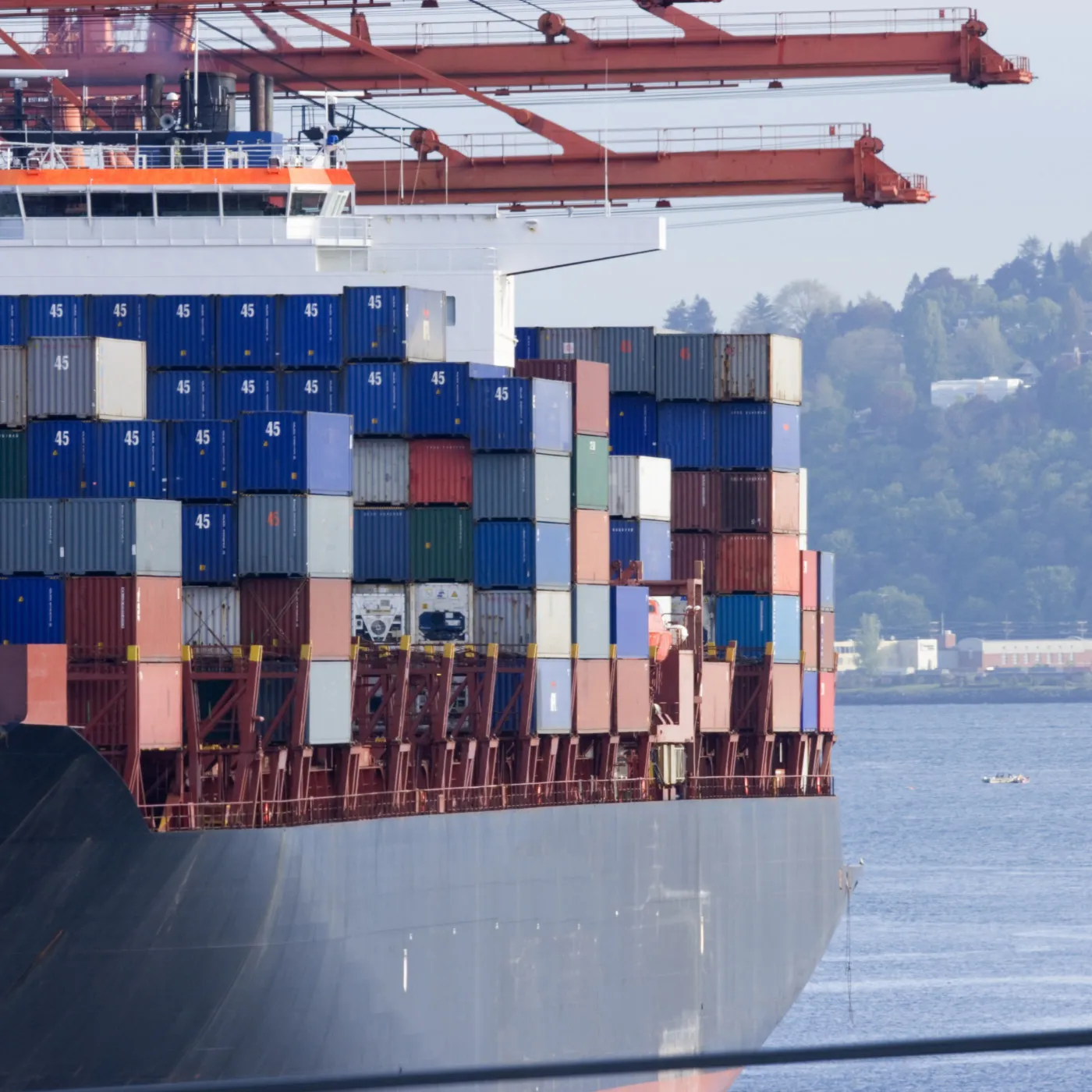
Maritime Transportation
Maritime fleets looking to reduce their emissions in the near term are likely to use biomass-derived renewable diesel, which can be used as a “drop-in” substitute in existing diesel engines with no modification. E-kerosene, fuels produced using electricity, hold similar potential. However, in the longer term, hydrogen is expected to play a key role in achieving truly zero-emission maritime transportation, whether directly as a fuel or as a feedstock for the production of hydrogen-derived fuels. The choice of fuel and propulsion technology for a given application is determined largely by range as well as cost and infrastructure requirements. While the production of hydrogen-derived fuels adds cost, they can be more easily transported and stored, and to varying extents they can utilize existing infrastructure and propulsion technologies, with different advantages for each. Other than the platinum dependency of fuel cells, there are no critical minerals requirements for these pathways.
Gaseous hydrogen: Ferries are a particularly appealing application for fuel cells using gaseous hydrogen, given their relatively short range and regular daily routes, and Washington is particularly well-suited for their development. Washington State Ferries (WSF) operates the largest ferry system in the U.S., with 21 ferries carrying nearly 20 million passengers annually across nine routes. Legislation passed in 2022 requires the state’s Department of Transportation to investigate the potential of hydrogen in WSF operations. Moreover, Washington-based All American Marine recently built and launched the world’s first gaseous hydrogen-powered fuel cell ferry, the aptly named 75-passenger Sea Change, which began regular operations in the San Francisco Bay this past summer after testing in the Puget Sound.
E-Methanol: E-methanol, sometimes referred to as “green methanol,” is made by combining hydrogen with CO2 captured from industrial smokestacks or directly from the air. Similar to ammonia, it is already a globally traded commodity used by the chemical industry, with established storage and transportation infrastructure in place. Moreover, unlike ammonia, it can be stored as a liquid at room temperature without additional compression requirements, and it is already used as a shipping fuel by some methanol carriers, giving it a higher level of technological readiness than liquid hydrogen or ammonia. However, e-methanol will likely be a more expensive fuel than ammonia, due to the high cost and limited availability of CO2 inputs, compared to the nitrogen used to produce ammonia.
Ammonia: Ammonia is a gaseous fuel produced from hydrogen and nitrogen using the established Haber-Bosch process, and it is already shipped all over the world as a key input for fertilizers. Existing large-scale production facilities and port infrastructure can thus be utilized, making this potentially the least expensive of the hydrogen-derived maritime fuels. It is more energy dense than hydrogen and is easier to liquefy, with minimal pressure required to store it as a liquid at room temperature. There is also ample experience handling and storing ammonia in ports and on ships, although its use as a fuel will require additional safety protocols due to its toxicity. While ship engines will need to be modified to burn ammonia, the Global Maritime Forum expects these engines to be commercially available by 2024, and the IEA notes that 66 orders for new-build shipping vessels in 2021 were “ammonia-ready.”
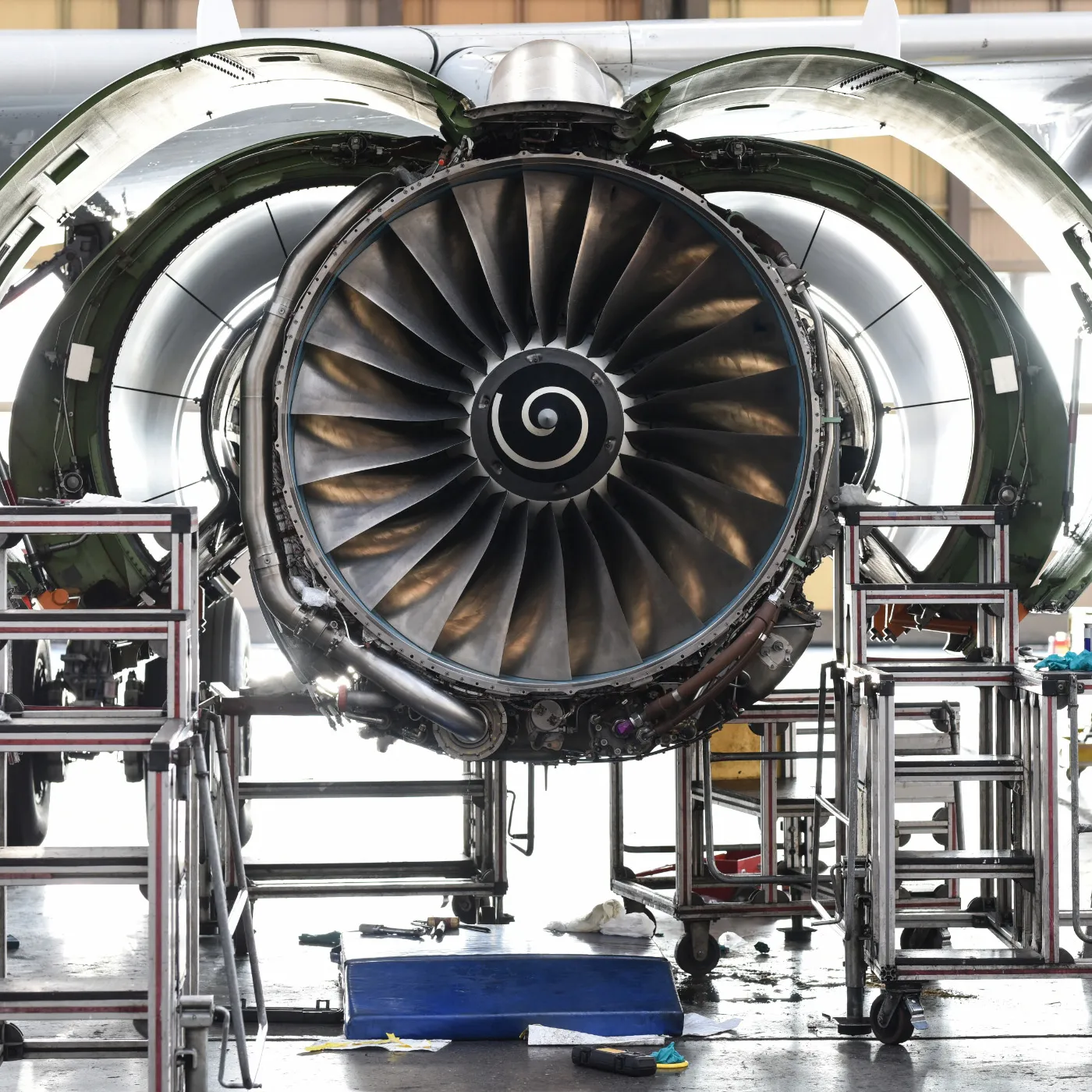
Aviation
Hydrogen is also expected to play a major role in decarbonizing the aviation segment, although as in maritime applications, it is expected that longer-range applications will use hydrogen as a feedstock to produce synthetic fuels with energy density and fuel-handling advantages. As in other transportation end-uses, fuel cell applications will depend on the use of platinum, and similarly to power generation applications described above, the direct combustion of hydrogen in jet turbines may require the use of alloys or coatings that use critical minerals such as chromium and yittria-stabilized zirconia (YSZ).
Liquid hydrogen: Whether it powers fuel cells or is combusted to drive a jet turbine, hydrogen is likely to be carried in liquefied form for aviation applications, due to its energy density advantages over gaseous hydrogen. That will require equipment for supercooling and storing it at airports and on aircraft at -253˚C, and because weight is a paramount concern for aircraft design, there will be a need for significant innovation in lightweight cryogenic tanks, fuel storage and delivery methods, and potential changes in aircraft design. One such innovative company, Universal Hydrogen, is demonstrating its swappable hydrogen fueling capsule design in test flights of a converted turboprop plane at Moses Lake, in collaboration with Seattle-based engineering company AeroTEC for the conversion, Everett-based MagniX for the electric motor, and Plug Power for the fuel cell. Everett, home to Boeing’s large-scale manufacturing facility, is also home to R&D facilities for ZeroAvia, another hydrogen fuel cell aviation startup that has received $115 million in venture funding from investors including Breakthrough Energy Ventures, Amazon’s Climate Pledge Fund, Alaska Airlines, and United Airlines. The International Council for Clean Transportation (ICCT) estimates that liquid hydrogen could power regional turboprop planes as well as narrow-body turbofan aircraft for short- to medium-haul flights of up to 3,400 km (2,100 miles) in range, accounting for roughly a third of passenger aviation traffic.
E-kerosene: A synthetic, carbon-neutral replacement for the kerosene fuel used in jet engines can be produced using hydrogen and CO2 captured from industrial sources or directly from the air. This adds fuel production costs compared to the direct use of hydrogen, but by eliminating the added weight and design challenges of cryogenic storage it is expected to be the only viable pathway for carbon-neutral long-haul flights of greater than 3,400 km. The IEA’s Net Zero by 2050 roadmap expects e-kerosene to be the main source of carbon-neutral aviation fuel by 2050, despite production costs as high as $130 to $300/barrel in 2050 (including $15 to $70 for CO2 costs), compared to fossil kerosene costs of just $25/barrel.
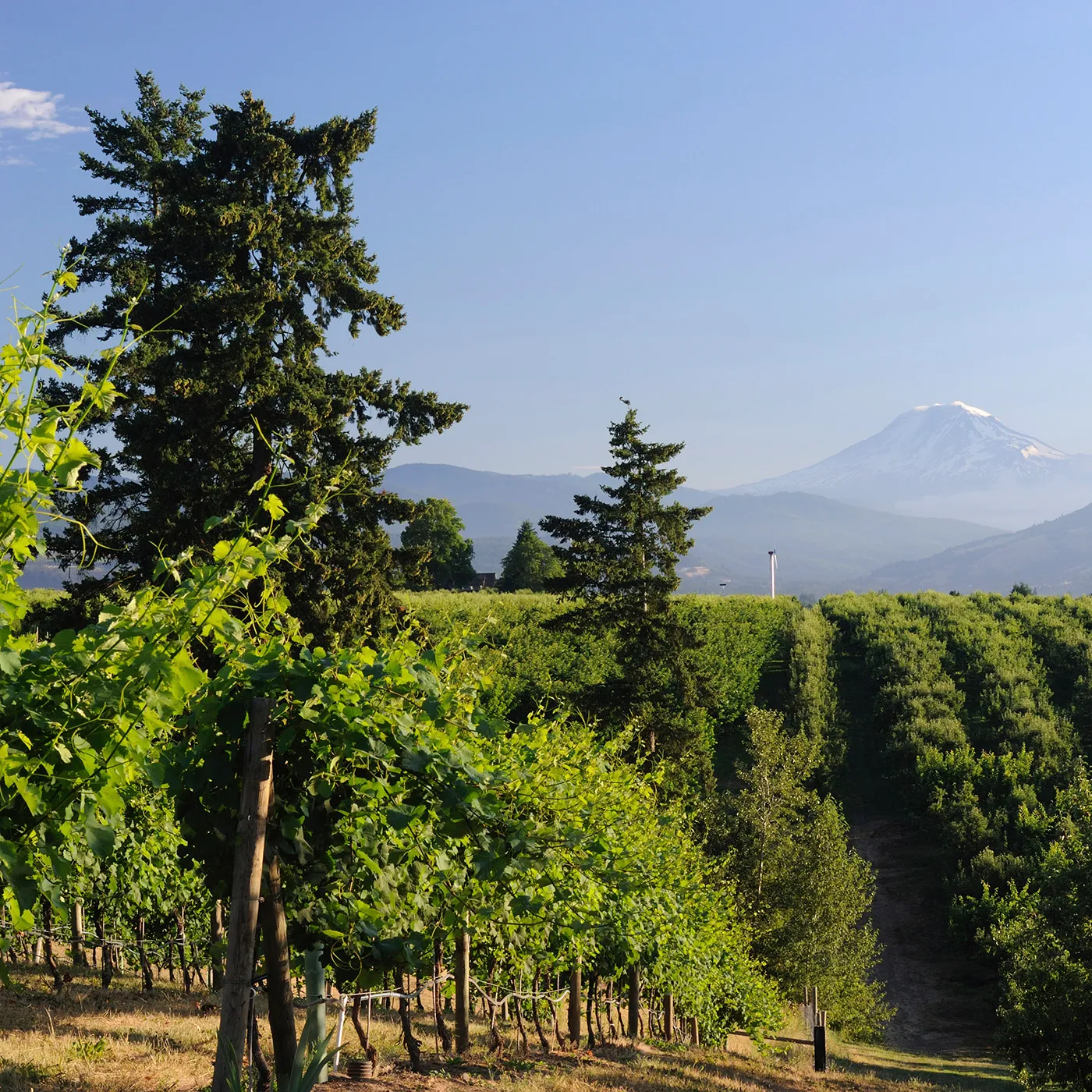
Agriculture
In addition to its potential as a zero-carbon shipping fuel, green ammonia’s first and most important near-term end use will be the decarbonization of fertilizer production. About 70 percent of global ammonia production is used to produce fertilizers, and, in contrast to the need to adapt engines and safety protocols to use green ammonia as a shipping fuel, green hydrogen can be used directly as a “drop-in” replacement for the fossil-derived hydrogen that is used in today’s large-scale fertilizer production plants. While this application is nascent today, IEA’s net zero scenario projects that green hydrogen will be the largest source of ammonia feedstock by 2050, with the remainder coming from fossil fuels with carbon capture or biomass-based processes.Washington is positioned to be a leader in this transition, with European fertilizer company Atlas Agro recently announcing plans to build its first green hydrogen-fueled production facility at the Horn Rapids Industrial Park in Richland. Located near the Pacific Northwest National Laboratory, the planned $1.1 billion facility will use hydrogen produced by 280 to 330 MW of electrolyzers. Atlas Agro reportedly hopes to power the facility with “new nuclear,” which could come from advanced nuclear projects such as the X-Energy installation being planned in Energy Northwest’s territory.
Looking Ahead: A More Secure Paradigm for Hydrogen Development
The development of a hydrogen hub requires the coordination of numerous stakeholders throughout the value chain, from zero-emission electricity suppliers to hydrogen producers, infrastructure providers, and end-users. Critical mineral supply chains are becoming increasingly salient as the industry begins to scale up, and potential disruptions are a key source of risk to project costs and timelines.
With its wealth of zero-emission resources, innovative companies, and major potential hydrogen end-users, the Pacific Northwest is well-positioned to be a leading hub for the U.S. hydrogen economy, as well as demonstrate ways to reduce or even eliminate these critical minerals risks.
Key focus areas include:
- Supply chain management: Depending on the technologies integrated into the hydrogen value chain, hydrogen hub development can face risks ranging from geopolitical tensions with China to mining sector instability in South Africa. Staying attuned to geopolitical and market dynamics, and working to ensure critical minerals and other inputs are sourced responsibility and from a relatively diverse pool of suppliers can help to mitigate risk and strengthen sourcing sustainability.
- Utilizing earth-abundant materials: Some technology choices in the hydrogen value chain can significantly reduce or eliminate critical minerals risks themselves, particularly in the upstream zero-emission electricity generation and storage segments. Some technologies such as hydropower and pumped hydro storage and flow batteries based on non-vanadium chemistries are essentially free from critical minerals risks. Other technologies offer reduced risks, such as LFP lithium-ion batteries compared to NMC chemistries, or advanced nuclear plants that can leverage conventional enriched uranium fuel instead of requiring HALEU. Scaling these technologies will be key to driving down costs and reducing dependencies.
- Recycling of critical minerals: The domestic recovery and recycling of critical minerals offers another avenue for increasing supply chain security. As discussed in the first part of this report, recycling of lithium-ion batteries could provide a substantial fraction of lithium, nickel, and cobalt needs, and investments in this sector are scaling up rapidly. Recycling of electrolyzers for their critical minerals, particularly platinum and iridium, is at a nascent stage but has similar potential to reduce requirements for imports. These efforts could potentially leverage existing approaches and infrastructure used to recycle platinum from catalytic converters, a well-established industry that will necessarily transition as internal combustion engine vehicles are phased out. This phaseout also presents an opportunity to recycle iridium from premium spark plugs.
- R&D for reducing critical minerals: On the hydrogen production side, there are fewer opportunities to avoid critical minerals requirements, and thus a greater need for research into methods of reducing these risks. Minimizing the amount of iridium required for PEM electrolyzer anodes is a particularly urgent priority, given the scarcity and cost of this platinum byproduct. A recently released Department of Energy R&D grant program is seeking to support research into anodes using <0.3 mg iridium (Ir)/cm. The Pacific Northwest innovation ecosystem has an opportunity to lead in this area, with the Pacific Northwest National Laboratory home to the Institute for Integrated Catalysts as part of its larger hydrogen research program. Other promising research avenues include the development of more durable AEM electrolyzers that avoid PGMs altogether in favor of nickel.
Concerns over energy security and climate change continue to fuel hydrogen development in the U.S. and around the world. In addition to hydrogen hubs under development in the U.S., supportive policies and development strategies are being advanced in China, the European Union, the UK, Japan, South Korea, Chile, Saudi Arabia, and others. Minimizing the critical minerals footprints of this nascent industry will be essential to ensuring that hydrogen realizes its potential to be a sustainable energy security solution, instead of contributing further to the geopolitical resource competition endemic in fossil fuels as well as clean energy industries.The Pacific Northwest’s combination of natural resources and innovative companies offers an opportunity to showcase a more secure paradigm for hydrogen development, underpin economic growth in the region, and accelerate the energy transition.
Read part 1 of this report: Mapping the vital inputs fueling the innovation economy
Publication date: March 2023
By John Atkinson (Contributor, FP Analytics) and Allison Carlson (Executive Vice President, FP Analytics & FP Events).

FP Analytics, the research and advisory division of Foreign Policy, produced this issue brief, which was commissioned and made possible with financial support from JCDREAM- the Joint Center for Deployment and Research in Earth Abundant Materials. Editorial control has been retained by FP Analytics.